Description

Servo presses in monoblock design are driven directly by torque motors. They deliver high torque values and are the right drive for dynamic forming processes. The lack of a flywheel and clutch / brake combination makes the presses flexible, energy efficient and reduces the maintenance required.
The pendular stroke mode is exceedingly energy efficient and permits operator-programmable slide strokes without any additional mechanical stroke adjustment. In addition, the pendular mode results in significantly higher stroke rates. Thanks to the operator-programmable time / travel motion sequences as well as the ability to provide rest times for in-die functions, processes such as welding and lasering can be integrated reliably into the press cycle.
Schuler builds servo presses in a monoblock design with three different standard sizes: 2,500 kN, 4,000 kN and 6,300 kN.
Your advantages
- Significant increase in productivity compared to conventionally driven mechanical presses
- Maximum production flexibility due to operator- programmable stroke heights and motion sequences
- Increased part quality and die life due to motion sequence optimally adapted to the specific forming requirements
- High reliability and availability for production
- Well suited for processing high-strength steels
- Short delivery times and optimized spare part management due to standardized modules
- Shorter die tryout times because of setup and tryout functions with handwheel
- Lower energy costs due to efficient drive solution
View
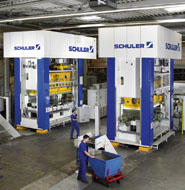
Servo presses in monoblock design with 4,000 kN press force per press
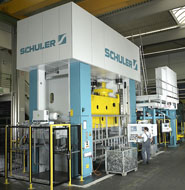
Servo press in monoblock design with modular electronic tri-axis transfer. Press force: 6,300 kN
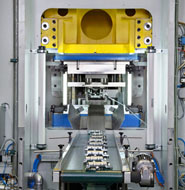
Increase of productivity due to energy efficient pendular stroke mode
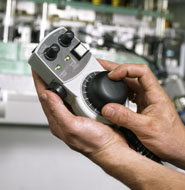
Flexible tryout with handwheel