Description
Hydroforming offers many advantages in high-volume production. This method for example involves forming of tubing with improved rigidity and strength in comples shapes - important safety factors in practical application. The roll bar in convertibles for example is not usually wanted by most drivers. As a result, the A-pillar must be sufficiently sturdy because in the event of a rollover it has to assume in part the function of the roll bar. The hydroforming method, since it involves work-hardening of the material, produces such a high degree of rigidity in the A-pillar that it is more than sufficient to assume the function of the roll bar. Schuler delivered the required hydroforming line for the BMW plant in Dingolfing. The complet production line consists of the following processing steps:
- Bending cell with automatic loading
- Reduction line
- Unit for application of lubricants
- A 5,000-metric-ton press with semi-automated die change
- Laser processing of component ends
All line components are interlinked by robots or pallet conveying systems and equipped with centralized control. This fully automated line can be seen in the short demonstration video.
View
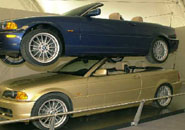
The strength of the A-pillar is sufficient even for four vehicles.
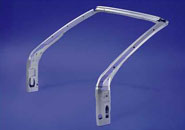
A-pillar lower and upper with cowl