Description
The working sequences before and after the actual forging are frequently performed on hydraulic presses. On hydraulic pre-form presses, pre-forms are generated so that there will be a mass distribution appropriate for the die. Having a pre-form with a good structure reduces the amount of material used and also reduces the forming forces required during forging. The die life is improved.
Following die forging, the flash is trimmed off and any required piercing and coining work is performed on hydraulic trimming and calibrating presses. These working sequences can either be combined in one die or performed consecutively in several stations.
Hydraulic forging presses are used wherever high forces and long working travel distances are required. This is revealed in numerous special applications up to press forces of 300.000 kN and working travel distances of 4 m. Examples include hot forging presses, piercing presses and presses for partial forging of fittings and thick-walled pipes.
Your advantages
- unlimited work energy permits maximum press force over the entire stroke
- infinite adjustment of the working stroke permits optimal adaptation of the press cycle to the forming process
- large slide stroke for long components provides an expanded range of possible products
- overloading of the press is not possible
- adaptation of the forming speed to the process produces superior workpiece quality and long die service life
View
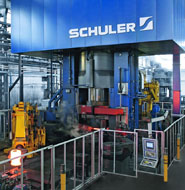
Hydraulic forging presses for forging railway wheels
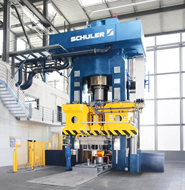
Hydraulic forging presses